
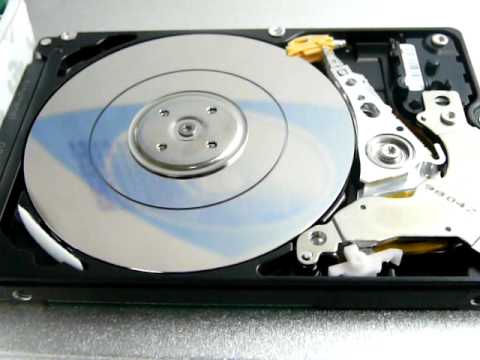
The surface of the platter is especially susceptible to finger prints with even the slightest touch. Any contamination can render the contaminated area of the platter unreadable. This video demonstrates how important platter alignment is… So if you or someone you know have disassembled your drive and removed the platters without maintaining their initial alignment, chances are your recovery just became considerably more difficult. The vertical and horizontal rotational alignments must be maintained at all times and there are only nanometers of tolerance. Data will probably be inaccessible, and may be unrecoverable, if the platter alignment is lost. Maintaining the alignment between the platters is crucial. The amount of data each platter holds and the mapping of the heads varies from model to model. Each surface will have a corresponding read-write head, and the data is spread out among each platter. On average, depending on capacity, you will find 1 to 3 platters in a hard drive. There can be as many as 4 in the more common drives, but that is typically the maximum. If you’ve ever seen the inside of a hard drive, you may notice that in some drives there are multiple platters. Maintaining Alignment Of Multiple Platters A special sensor examines the platter surface for any remaining defects. The platter is then allowed to cure and receives a final buff to remove any defects in the surface. Finally, a thin lubricant layer, approximately one nanometer is applied by dipping the platter into a solution. There is also a protective coating that is carbon based and is applied in the same manner. The coating itself is comprised of mostly non-magnetic metallic alloys which is very complex in structure. Vacuum deposition is a wonder all on it’s own, as this process deposits material, atom by atom or molecule by molecule onto a solid surface. After the platter is machined, it is then coated using a vacuum deposition process called magnetron sputtering. The actual platter is most often made of aluminum or glass substrate. It is possible that in the future, drive manufacturers may use different systems to create the magnetic regions. It is these magnetic grains which become magnetized when data is written to the drive. Today, each of these magnetic regions within the hard drive is composed of a few hundred magnetic grains. The materials which make up the magnetic layer are usually a cobalt-based alloy. This comes to about 100 billion bits (100 gigabits) per square inch of hard drive platter area. A binary region on a hard drive platter (as of 2006) is about 200-250 nanometers wide (within the radial direction of the platter) and extends about 25-30 nanometers in the down-track direction.
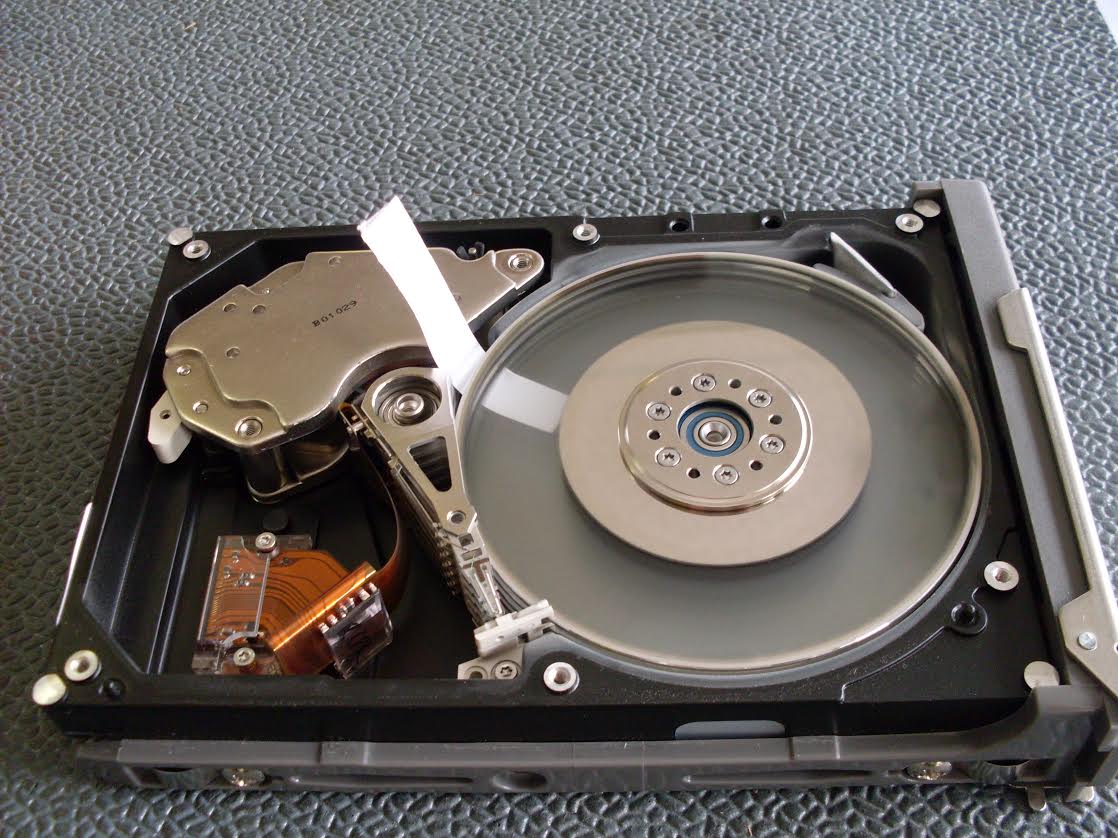
Each of these regions makes up a single binary unit of information. Click here to read more about the complexity of modern hard drives. When talking about hard drives, it’s important to note that everything is measured on a microscopic level. The magnetic surface of each platter is divided into magnetic regions less than a micrometer in size. The image to the left illustrates what a platter looks like after it has been scored by a head crash.

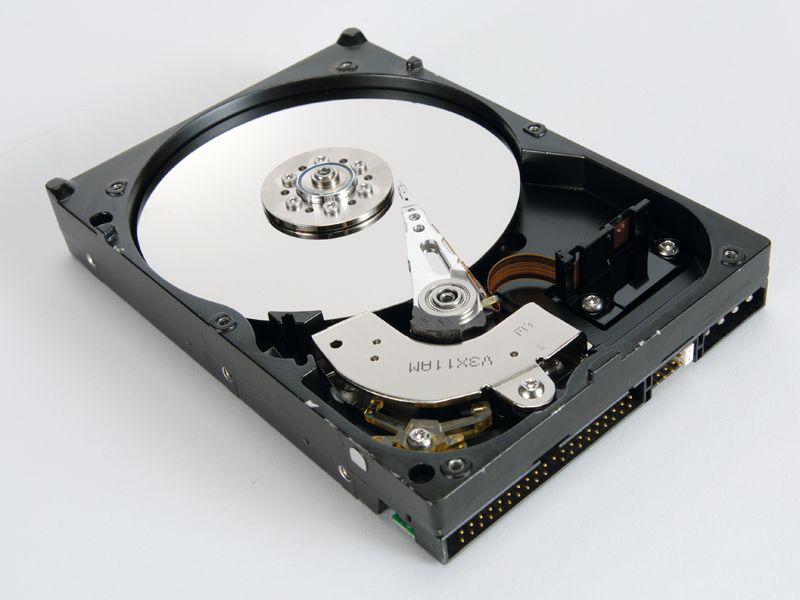
The platters of a hard drive actually hold your data.
